
Les plateformes pétrolières offshore représentent l'un des plus grands défis de l'ingénierie moderne. Ces structures colossales, véritables usines flottantes, doivent résister aux conditions les plus extrêmes tout en assurant une production d'hydrocarbures continue et sécurisée. De la conception initiale au démantèlement final, chaque étape de leur cycle de vie fait appel à des technologies de pointe et nécessite une expertise multidisciplinaire. Face aux enjeux environnementaux croissants, l'industrie offshore doit aujourd'hui concilier performance opérationnelle et responsabilité écologique. Plongeons au cœur de ces titans des mers pour comprendre les prouesses techniques et les défis qui façonnent leur avenir.
Conception technique des plateformes pétrolières offshore
La conception d'une plateforme pétrolière offshore est un processus complexe qui nécessite la prise en compte de nombreux facteurs. Les ingénieurs doivent créer des structures capables de résister à des conditions météorologiques extrêmes, tout en assurant la sécurité des travailleurs et l'efficacité de la production. Le choix du type de plateforme dépend principalement de la profondeur d'eau, des conditions environnementales et des caractéristiques du gisement à exploiter.
Structures jackup vs. semi-submersibles : analyse comparative
Les plateformes auto-élévatrices, ou jackup
, sont utilisées dans des eaux peu profondes, généralement jusqu'à 150 mètres de profondeur. Elles reposent sur des jambes rétractables qui peuvent être abaissées jusqu'au fond marin. Les plateformes semi-submersibles, quant à elles, flottent partiellement immergées et sont maintenues en position par des systèmes d'ancrage ou de positionnement dynamique. Elles sont adaptées aux eaux plus profondes, pouvant opérer jusqu'à 3000 mètres de profondeur.
Voici un tableau comparatif des deux types de structures :
Caractéristique | Jackup | Semi-submersible |
---|---|---|
Profondeur d'eau | Jusqu'à 150m | Jusqu'à 3000m |
Mobilité | Remorquable | Auto-propulsée ou remorquable |
Stabilité | Très stable une fois installée | Sensible aux mouvements de la mer |
Coût | Moins élevé | Plus élevé |
Systèmes d'ancrage et positionnement dynamique
Le maintien en position d'une plateforme offshore est crucial pour la sécurité et l'efficacité des opérations. Les systèmes d'ancrage traditionnels utilisent des chaînes ou des câbles reliés à des ancres enfouies dans le fond marin. Pour les eaux très profondes ou les conditions météorologiques particulièrement difficiles, le positionnement dynamique est souvent préféré. Ce système utilise des propulseurs contrôlés par ordinateur pour maintenir automatiquement la position de la plateforme.
L'efficacité du positionnement dynamique repose sur des capteurs sophistiqués qui mesurent en temps réel les forces exercées par le vent, les vagues et les courants. Ces données sont traitées par des algorithmes complexes qui ajustent en continu la poussée des propulseurs. Cette technologie permet une précision remarquable, maintenant la plateforme dans un rayon de quelques mètres, même dans des conditions difficiles.
Ingénierie des modules de forage et de production
Les modules de forage et de production sont le cœur opérationnel d'une plateforme pétrolière. Leur conception doit optimiser l'espace disponible tout en assurant une circulation fluide du personnel et des matériaux. L'ingénierie de ces modules fait appel à des logiciels de modélisation 3D avancés qui permettent de simuler l'agencement des équipements et d'identifier les potentiels conflits avant la construction.
Un aspect crucial de la conception des modules est la gestion des risques. Chaque composant est analysé pour son potentiel de défaillance et ses conséquences. Des systèmes redondants sont mis en place pour les équipements critiques, assurant la continuité des opérations même en cas de panne. La sécurité du personnel est également primordiale, avec des chemins d'évacuation clairement définis et des zones de refuge pressurisées en cas d'urgence.
Conception parasismique et résistance aux ouragans
Dans les zones sismiques actives ou sujettes aux ouragans, la conception des plateformes doit intégrer des mesures de protection spécifiques. Les ingénieurs utilisent des modèles mathématiques complexes pour simuler les effets des tremblements de terre et des vents violents sur la structure. Des amortisseurs et des systèmes d'isolation sismique sont intégrés pour absorber les vibrations et réduire les contraintes sur la plateforme.
Pour résister aux ouragans, les plateformes sont conçues pour supporter des vagues pouvant atteindre 30 mètres de hauteur et des vents de plus de 200 km/h. La forme de la structure est optimisée pour réduire la résistance au vent, tandis que des renforts structurels supplémentaires sont ajoutés aux points critiques. Des systèmes de ballast automatisés permettent également d'ajuster la stabilité de la plateforme en fonction des conditions météorologiques.
Processus de construction et d'installation en mer
La construction et l'installation d'une plateforme pétrolière offshore sont des opérations d'une complexité logistique et technique exceptionnelle. Ces processus nécessitent une coordination précise entre de nombreux acteurs et l'utilisation d'équipements spécialisés de grande envergure. L'objectif est de minimiser le temps de construction sur site, réduisant ainsi les coûts et les risques associés aux opérations en mer.
Fabrication modulaire dans les chantiers navals
La construction des plateformes pétrolières suit généralement une approche modulaire. Les différentes sections de la plateforme sont fabriquées simultanément dans des chantiers navals spécialisés, souvent situés dans différentes parties du monde. Cette méthode permet d'optimiser les délais de production et de bénéficier des expertises spécifiques de chaque chantier.
Chaque module peut peser plusieurs milliers de tonnes et contenir des équipements pré-installés, des systèmes électriques et des tuyauteries. La précision est cruciale lors de la fabrication, car les modules doivent s'assembler parfaitement une fois sur site. Des techniques de soudage avancées et des contrôles qualité rigoureux sont mis en œuvre pour garantir l'intégrité structurelle de chaque composant.
Transport maritime des structures : navires heavy-lift
Le transport des modules de plateforme vers le site d'installation est une opération délicate qui requiert des navires spécialisés appelés heavy-lift. Ces navires sont capables de transporter des charges extrêmement lourdes et volumineuses. Certains, comme le Pioneering Spirit, peuvent soulever jusqu'à 48 000 tonnes en une seule opération.
La planification du transport prend en compte de nombreux facteurs, notamment les conditions météorologiques, les routes maritimes et les réglementations internationales. Les modules sont solidement arrimés et protégés contre les intempéries. Des systèmes de surveillance en temps réel permettent de contrôler la stabilité du navire et l'intégrité de la cargaison tout au long du voyage.
Techniques d'installation : méthode float-over vs. levage
L'installation des modules sur la structure de base de la plateforme peut se faire selon deux méthodes principales : le float-over et le levage. La méthode float-over consiste à positionner le module entre les jambes de la plateforme à l'aide d'un navire semi-submersible, puis à l'abaisser en place en ajustant le ballast du navire. Cette technique est particulièrement adaptée pour les modules très lourds.
Le levage, quant à lui, utilise des grues géantes montées sur des navires spécialisés. Cette méthode offre plus de flexibilité mais est limitée par la capacité de levage des grues. Les opérations de levage sont minutieusement planifiées et simulées en amont pour anticiper tous les scénarios possibles.
La précision lors de l'installation est cruciale. Un écart de quelques centimètres peut avoir des conséquences importantes sur l'alignement des systèmes et la sécurité globale de la plateforme.
Raccordement sous-marin et mise en service
Une fois la structure principale en place, l'étape suivante consiste à réaliser les raccordements sous-marins. Des robots sous-marins téléguidés (ROV) sont utilisés pour connecter les conduites et les câbles entre la plateforme et les puits de forage. Ces opérations se déroulent souvent à des profondeurs considérables et nécessitent une expertise technique pointue.
La mise en service de la plateforme est une phase critique qui peut durer plusieurs mois. Chaque système est testé individuellement puis dans son ensemble pour s'assurer de son bon fonctionnement. Des procédures de sécurité rigoureuses sont mises en place et le personnel est formé aux protocoles d'urgence. Ce n'est qu'après cette phase intensive de tests et de vérifications que la production peut véritablement commencer.
Défis écologiques et solutions innovantes
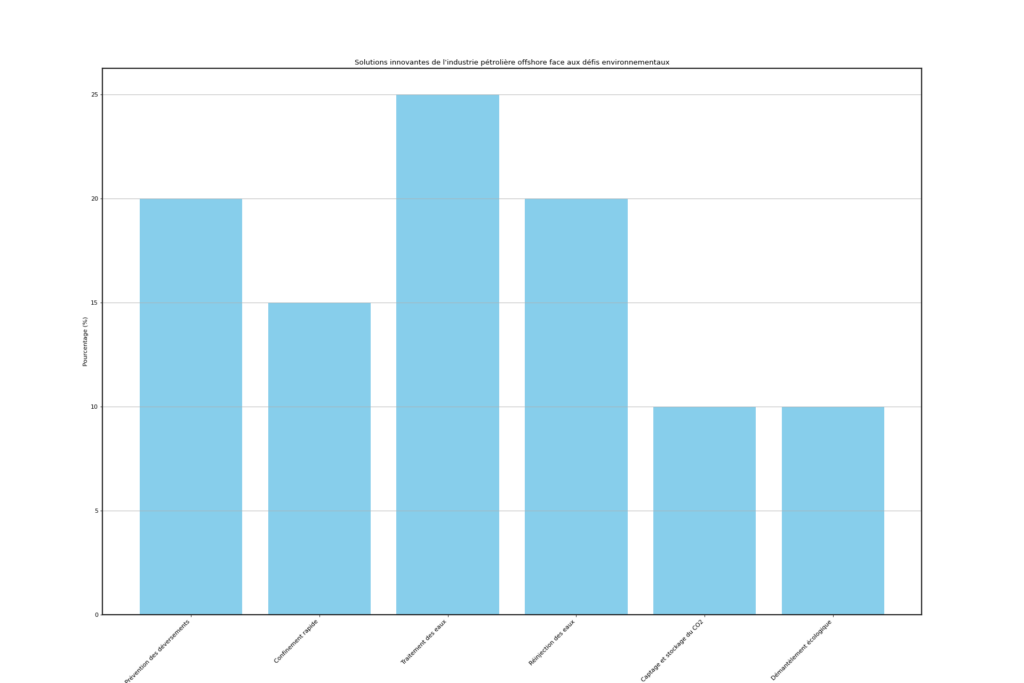
L'industrie pétrolière offshore fait face à des défis environnementaux majeurs. La pression réglementaire et sociétale pousse les opérateurs à adopter des pratiques plus respectueuses de l'environnement. Les innovations technologiques jouent un rôle crucial dans la réduction de l'impact écologique des plateformes pétrolières.
Prévention des déversements : BOP et systèmes de confinement
La prévention des déversements d'hydrocarbures est une priorité absolue. Le Blowout Preventer
(BOP) est un dispositif de sécurité critique installé sur la tête de puits pour contrôler la pression et prévenir les éruptions incontrôlées. Depuis l'accident de Deepwater Horizon en 2010, les BOP ont fait l'objet d'améliorations significatives, notamment avec l'ajout de systèmes de déclenchement redondants et de capteurs plus sophistiqués.
En complément du BOP, des systèmes de confinement rapide ont été développés. Ces dispositifs peuvent être déployés rapidement en cas de fuite pour capter les hydrocarbures avant qu'ils n'atteignent la surface. Certains systèmes, comme le Subsea Containment Assembly, peuvent être installés directement sur un puits en éruption pour rediriger le flux vers des navires de surface.
Traitement des eaux de production et réinjection
Les eaux de production, extraites avec le pétrole, représentent un défi environnemental majeur. Ces eaux contiennent des hydrocarbures résiduels et divers contaminants. Des technologies avancées de traitement, comme la flottation à gaz dissous et la filtration membranaire, sont utilisées pour purifier ces eaux avant leur rejet ou leur réinjection.
La réinjection des eaux de production dans le réservoir est une pratique de plus en plus courante. Elle permet non seulement de réduire l'impact environnemental mais aussi d'améliorer la récupération du pétrole. Des études montrent que la réinjection peut augmenter le taux de récupération de 5 à 15%, prolongeant ainsi la vie productive du champ.
Réduction des émissions : captage et stockage du CO2
Les émissions de gaz à effet de serre sont un enjeu majeur pour l'industrie offshore. Le captage et le stockage du CO2 (CSC) émergent comme une solution prometteuse. Cette technologie consiste à capturer le CO2 produit par les opérations, à le comprimer et à l'injecter dans des formations géologiques profondes pour un stockage à long terme.
Le projet Sleipner en mer du Nord, opéré par Equinor, est un exemple pionnier de CSC offshore. Depuis 1996, il a permis de stocker plus d'un million de tonnes de CO2 par an dans un aquifère salin. D'autres projets similaires se développent, comme Northern Lights en Norvège, qui vise à créer une infrastructure de transport et de stockage de CO2 à grande échelle.
Démantèlement éco-responsable : cas du champ brent
Le démantèlement des plateformes en fin de vie pose des défis environnementaux et techniques considérables. Le cas du champ Brent en mer du Nord, exploité par Shell, illustre la complexité de ces opérations. Le plan de démantèlement, d'un coût estimé à plusieurs milliards de dollars, prévoit le retrait de quatre plateformes géantes, totalisant plus d'un million de tonnes de matériaux.
L'approche adoptée vise à maximiser le recyclage des matériaux et à minimiser l'impact sur l'écosystème marin. Des techniques innovantes sont employées, comme l'utilisation de single lift vessel capable de retirer des structures entières en une seule opération. La question du devenir des bases en béton, trop lourdes pour être retirées, fait l'objet de débats et d'études d'impact approfondies.
Le démantèlement responsable des plateformes offre une opportunité unique d'étudier l'impact à long terme des structures offshore sur la biodiversité marine et de développer de meilleures pratiques pour les futurs projets.
Réglementations et normes de sécurité internationales
L'industrie pétrolière offshore est soumise à un cadre réglementaire strict et en constante évolution. Ces réglementations visent à garantir la sécurité des opérations, la protection de l'environnement et la santé des travailleurs. Elles sont
établies au niveau international pour assurer une harmonisation des pratiques à l'échelle mondiale.
Standards API et ISO pour la conception offshore
L'American Petroleum Institute (API) et l'Organisation internationale de normalisation (ISO) jouent un rôle crucial dans l'établissement de normes pour l'industrie offshore. Les standards API, tels que l'API RP 2A pour la conception des plateformes fixes, sont largement adoptés dans le secteur. Ces normes couvrent tous les aspects de la conception, de la fabrication à l'installation, en passant par l'exploitation et la maintenance.
L'ISO 19900 est une série de normes spécifiquement dédiées aux structures offshore. Elle fournit des lignes directrices pour la conception, la construction et l'exploitation des plateformes pétrolières. Ces normes sont régulièrement mises à jour pour intégrer les dernières avancées technologiques et les retours d'expérience de l'industrie.
Directives MARPOL pour la protection marine
La Convention internationale pour la prévention de la pollution par les navires (MARPOL) s'applique également aux plateformes offshore. L'annexe I de MARPOL définit des règles strictes concernant la prévention de la pollution par les hydrocarbures. Elle impose notamment des limites sur les rejets d'eau de production et exige l'utilisation de séparateurs eau-huile performants.
Les opérateurs offshore doivent également se conformer à l'annexe V de MARPOL, qui traite de la gestion des déchets. Cette réglementation impose des restrictions sur le rejet de déchets en mer et encourage le recyclage et la valorisation des déchets à terre. Comment les compagnies pétrolières gèrent-elles ces contraintes environnementales croissantes tout en maintenant leur rentabilité ?
Certifications SOLAS et exigences de sauvetage en mer
La Convention internationale pour la sauvegarde de la vie humaine en mer (SOLAS) s'applique aussi aux plateformes offshore. Elle définit des exigences strictes en matière d'équipements de sauvetage et de procédures d'urgence. Les plateformes doivent être équipées de canots de sauvetage, de radeaux gonflables et de gilets de sauvetage en nombre suffisant pour l'ensemble du personnel.
Les exercices d'évacuation réguliers sont obligatoires et les équipages doivent être formés aux procédures de sauvetage en mer. Des systèmes d'alerte sophistiqués sont mis en place pour détecter rapidement tout incident et déclencher les protocoles d'urgence. La sécurité du personnel est comparable à celle d'un navire de croisière, avec des exigences parfois encore plus strictes compte tenu des risques spécifiques à l'industrie pétrolière.
Avancées technologiques et plateformes du futur
L'industrie offshore est en constante évolution, poussée par la nécessité d'exploiter des gisements toujours plus profonds et difficiles d'accès. Les avancées technologiques transforment radicalement la conception et l'exploitation des plateformes pétrolières, ouvrant la voie à des structures plus efficaces, plus sûres et plus respectueuses de l'environnement.
Plateformes autonomes et systèmes de contrôle à distance
L'automatisation gagne du terrain dans l'industrie offshore. Des plateformes de plus en plus autonomes sont développées, capables de fonctionner avec un personnel réduit, voire sans présence humaine permanente. Ces installations sont équipées de capteurs avancés et de systèmes de contrôle à distance qui permettent une surveillance 24h/24 depuis des centres opérationnels à terre.
Cette évolution vers l'autonomie présente plusieurs avantages. Elle réduit les risques pour le personnel en limitant l'exposition aux environnements dangereux. Elle permet également d'optimiser les coûts d'exploitation en réduisant les rotations d'équipages et les besoins en logistique. Cependant, elle soulève aussi des défis en termes de cybersécurité et de fiabilité des systèmes de communication à longue distance.
Integration de l'ia pour l'optimisation des opérations
L'intelligence artificielle (IA) révolutionne la gestion des opérations offshore. Des algorithmes d'apprentissage automatique analysent en temps réel des quantités massives de données provenant des capteurs de la plateforme pour optimiser la production, prédire les besoins de maintenance et détecter les anomalies avant qu'elles ne deviennent critiques.
Par exemple, l'IA peut ajuster en continu les paramètres de forage en fonction des conditions géologiques rencontrées, maximisant ainsi l'efficacité de l'extraction. Elle peut également prédire les pannes d'équipements, permettant une maintenance prédictive qui réduit les temps d'arrêt et prolonge la durée de vie des installations. L'IA est à l'offshore ce que le GPS est à la navigation : un outil indispensable pour naviguer dans la complexité des opérations modernes.
Concepts de plateformes flottantes pour l'éolien offshore
L'expertise acquise dans la conception de plateformes pétrolières flottantes trouve aujourd'hui de nouvelles applications dans le domaine des énergies renouvelables, notamment l'éolien offshore. Des concepts innovants de plateformes flottantes pour éoliennes sont en cours de développement, permettant l'installation de parcs éoliens dans des eaux plus profondes, là où les fondations fixes ne sont pas économiquement viables.
Ces plateformes flottantes pour éoliennes s'inspirent directement des technologies développées pour l'industrie pétrolière, comme les structures semi-submersibles ou les plateformes à lignes tendues (TLP). Elles ouvrent de nouvelles perspectives pour l'exploitation de l'énergie éolienne en haute mer, où les vents sont plus forts et plus constants. Cette convergence technologique entre les secteurs pétrolier et éolien illustre comment l'expertise offshore peut contribuer à la transition énergétique.
L'avenir de l'offshore ne se limite pas à l'extraction d'hydrocarbures. Les technologies développées pour les plateformes pétrolières pavent la voie à une nouvelle génération d'installations maritimes multi-usages, capables de produire de l'énergie renouvelable, de dessaler l'eau de mer ou même d'héberger des centres de données sous-marins.
En conclusion, la construction de plateformes pétrolières reste un défi technique et écologique majeur. Les innovations constantes dans ce domaine ne visent pas seulement à améliorer l'efficacité et la sécurité des opérations, mais aussi à réduire l'empreinte environnementale de l'industrie offshore. Alors que le monde se tourne vers des sources d'énergie plus durables, l'expertise acquise dans la conception et l'exploitation des plateformes pétrolières jouera un rôle crucial dans le développement des infrastructures énergétiques du futur. Qu'il s'agisse d'extraire du pétrole ou de capter l'énergie du vent, les océans continueront d'être un terrain d'innovation technologique pour les décennies à venir.
Pour en savoir plus sur les dernières avancées dans la conception et la construction des plateformes offshore, n'hésitez pas à consulter cet article détaillé sur comment construire plateformes pétrolières.